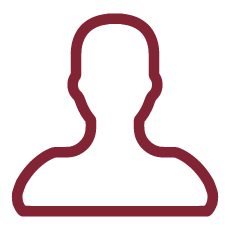
In recent years, wind energy has become one of the most important and promising sources of renewable energy, which demands additional transmission capacity and better means of maintaining system reliability. As wind power continues its rapid growth worldwide, offshore wind farms are likely to comprise a significant portion of the total production of wind energy and may even become a sizable contributor to the total electricity production in some countries.
This work studies multi-physic numerical modeling of floating offshore wind turbines (FOWT) with spar-buoy support platform using finite element method (FEM), computational fluid dynamics (CFD), blade element momentum (BEM) and other theories and methods to analyze the multi-physic model of the complete system of FOWT in 2D. During the project, efforts will be made to better understand the system properties of floating offshore wind turbines and to improve both numerical and physical modeling techniques. The goal of this study is comparing between different type of supporting platform for deep-water (¿200 meters) and optimum model of a spar-buoy supported platform for a FOWT. Ansys commercial code will use for modeling multi-physic behavior of offshore wind turbine (OWT). All the wind turbine response simulations in this study will run using the program, FAST (Fatigue, Aerodynamics, Structures, and Turbulence), developed at the National Renewable Energy Laboratory. The NREL 5 MW baseline wind turbine model, developed to represent a typical utility-scale multi-megawatt wind turbine for offshore applications, is considered in the present study. The turbine model is a conventional three-bladed variable-speed, collective pitch-controlled upwind machine. It was developed to support concept studies.
Reliability has increased since the first inland prototypes were installed, which has led to the deployment of wind turbines in remoter and harsher environments. Experience from the oil and gas industry in offshore installations and foundations has allowed the wind turbine to go offshore, where the wind is stronger. In [1], an analysis shows that offshore wind farms are being built further from the coast and in
deeper waters. Since 2011, the average offshore wind farm water depth has increased from 22.8 meters to 25.3 meters, and the distance to shore has increased from 23.4 km to 33.2 km.
Today, the wind turbine is a commercial product which is competing against other sources of energy, such as gas and coal. This competition has driven a constantly developing design and optimization process aiming at reducing costs and improving efficiency to reduce the total cost of the energy. Partly as a response to this, the size of wind turbines has increased from kilowatts to multi-megawatts. This trend is supported in [2], which shows that wind turbines are feasible even at 20 MW with rotor diameters of 252 meters.
In [3], the advantages of siting wind turbines offshore are analyzed. The average offshore wind speed is typically 20% greater than onshore. The ambient turbulence is less, which prolongs the turbine¿s lifetime. Furthermore, issues related to noise and visual impact are reduced.
Depending on the water depth, a variety of foundations have been used. From an economic point of view, the deep-water foundations are the most expensive, however, the expected wind speeds are higher and thus the expected electrical power production is higher. The monopile foundation is a popular example of
offshore deployment. However, this foundation is economically limited to shallow water depths below 30 meters. Other concepts of foundations, such as the jacket and tripod, are designed for water depths in the range of 25¿50 meters. However, researches show that the spar-buoy platform has better performance in deep-water ( higher than 150m).
There are some relevant reasons, to move wind energy production from land to offshore:
- Better wind resources
- Offshore constructions have almost no restrictions concerning noise and visual impact.
- The limited availability of land, especially in Europe, suggests the exploitation of the sea.
- The possible involvement of new competitors, such as Oil and Gas companies (O&G), could bring new values in the market, in terms of both investments and technology.
To solving the problem of complexity of the floating system include supporting platform and wind turbine should consider the different part of materials.
In the present article, taking input the NREL 5 Mw turbine and spar-buoy support structure in deep-water ( ¿200 m) concept will investigate.
Also, if these days a lot of codes and computational programs have been developed for OWTs design, very few numerical tools are available for FOWTs design. There is a necessity of producing reliable and realistic numerical tools for the preliminary design and analysis of OWTs (and particularly of spar buoy-supported typologies). This is exactly what is pursued in this project, which focuses to model spar-buoy supporting platform in 2D using FEM and CFD methods in deep water ( ¿200 meters).
The novelty of the model will be that it is fully multi-physical modeling of floating. Fluid-structure interaction (wave loads on spar-buoy support structure) and wind aerodynamic loads on wind turbine will model to the understanding better performance of floating support structure. Another innovation of this study is model buoyancy behavior of support structure, which is totally different from fixed support for wind turbine and oil and gas industry support structures, floating support structure must provide enough buoyancy to sustain the wind turbine weight plus its own weight. It also must provide enough rotational stability to prevent the system from capsizing and good wave response motions to prevent the structure from experience large dynamic loads or compromise the performance of the wind.