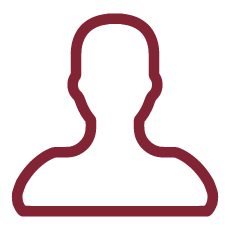
Over the past decades, the widespread use of glass fibres within polymeric matrix composite materials has significantly increased, leading to a strong interest in greater eco-sustainability due to the limited disposal options of these materials at the end of their life. For this reason, the production of bio-composite materials, using sustainable matrices or natural reinforcing fibres, has recently been a cornerstone of many research fields. Basalt fibres, due to their volcanic rock-based origin, are considered natural fibres and a greener alternative to glass fibres. The challenge for the development of these new composite materials is the optimization of the load transfer between the fibres and the matrix, through an adequate interface. A recent strategy for tailoring the interface while promoting additional functionalities involves the direct growth of carbon nanostructures (CNs) on the surface of fibres. In this regard, a current limitation is the high temperature step typical of thermal Chemical Vapor Deposition (CVD) growth that reduces the mechanical properties of the underlying fibres. In this research project, a new route for direct growth of CNs on natural basalt fibres is proposed, by combining new metal catalysts and plasma-enhanced CVD technology. The research will address process optimization and a systematic investigation of the complex relationships between process parameters and the mechanical and interfacial properties of the underlying fibres. The resulting hierarchical and multifunctional fibres will be exploited not only as reinforcing constituents in structural composites but also as effective materials in environmental remediation applications.
Carbon-based nanostructures (CNs), such as carbon nanotubes and graphene, have triggered enhancements to industrial applications such as advanced displays, sensors, and aerospace composites mainly driven by CNs integrated via transfer methods. However, there is a remarkable under-exploited potential for applications that need direct growth of CNs on substrates [1]. Until now, candidate substrates have been limited by the high temperatures (usually greater than 700°C) and catalyst materials (e.g. Fe, Ni, and Co) that are typically required. Even for carbon fibres, most of the previous studies pointed out a degradation of the initial mechanical properties [2], which is more severe for other fibres, such glass and quartz [3], where strength decreases up to 50% were reported when using a Fe/Ni bimetallic catalyst. The interplay between temperature, reactive gases and catalytic particles during the CNs growth is responsible for this phenomenon, but not conclusive studies exist. The need to lower the growth temperature to allow for a more economically viable and scalable process has traditionally involved the use of low pressures and plasma assistance. In this research project, we propose the use of alternative catalysts to trigger the growth of CNs at low temperature and preserve the mechanical properties of the pristine fibres. Recently, Na-catalysed CNs growth has been demonstrated on carbon fibres at temperatures as low as 400°C [4] by using low-cost precursors, such as NaCl, NaHCO3, Na2CO3 and NaOH. Also copper is a promising option for CNs growth at low temperatures [5], but the effect of various CVD growth parameters, such as temperature, catalyst composition, process gas mixture, presence or not of plasma, has not been systematically studied and correlated with the mechanical and interfacial properties of the underlying fibres. In addition, the present project will include process tailoring, catalyst solution modifications (e.g., investigating the pH effects, times and concentrations), and post-growth treatments to tune the degree of graphitization and morphology of the resulting CNs and their effects on the treatment of environmental pollutants.
To this aim, PE-CVD process will be employed for low temperature synthesis of CNs on basalt fibres. The possibility of growing CNs at reduced temperatures (600°C). The low temperature growth of CNs will be carried out at the Sapienza CVD facility that, through a fine tuning of CVD process parameters, has already successfully synthesized vertically aligned CNs (VA-CNs) with controllable diameters (5-30nm), lengths (5-300micron) and densities (10^8-10^10CNs/cm2) on different substrates (i.e., silicon and fused silica) [6-8]. A SEM image of a typical VA-CNs growth on a fused silica substrate is shown in Fig.2 (previous section).
Moreover, by means of such CVD chamber, uniform growth of VA-CNs was performed also on basalt fabrics (Fig.3, previous section) without involving the deposition of any additional catalyst film. Notably, in that case, the yield and density of the as-produced CNs are comparable, and in some cases higher, with that of similar CNs grown on convectional substrates.
However, the synthesis of VA-CNs on basalt fabrics was performed by conventional thermal CVD technique at temperatures >600°C that compromise the mechanical properties of the fibres.
Therefore, the here-proposed technology consisting in the direct growth of CNs on basalt fibres via PE-CVD, represents a highly innovative and likely decisive approach to develop novel hierarchical composite materials with added mechanical, thermal, electrical and environmental remediation performances. Furthermore, the possibility of modulating the diameter, density, uniformity and alignment of the CNs by properly adjusting PE-CVD parameters (i.e., working plasma power, reaction temperature, gas pressure and flow rate, size of the nanoparticle catalysts) will permit a fine control of the functionalities of the resulting materials.
As regards the environmental application, commercial materials are often expensive and quickly undergo degradation, with the risk of a potential release of pollutants to the environment. The application in electrochemical system of durable materials can offer the opportunity to combine environmental remediation to renewable energy production.
[1] A. Salas et al., Scientific Reports,1,5000, 2021.
[2] F An et al, Mater. & Des.,33,197-202, 2012.
[3] H.G. De Luca et al, Compos. Sci. Technol.,198,108275, 2020.
[4] R. Li et al., Angew Chem Int Ed Engl.,58(27),9204-9209, 2019.
[5] L.H. Acauan et al, Carbon,177,1-10,2021.
[6] I. Rago, Advanced Biosystems,3(5),1800286,2019.
[7] N. P. Pampaloni et al,1-16,2020.
[8] G. Cavoto, J. Phys.: Conf. Ser. ,1468(1),012232,2020.