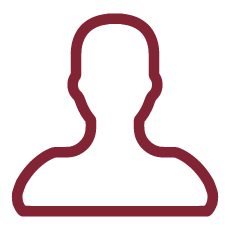
La Mass Customization è il nuovo approccio produttivo seguito dalle imprese volto a mantenere i vantaggi produttivi della produzione di massa, ma consentendo in aggiunta una personalizzazione del prodotto da parte del cliente. In quest¿ottica la stampa 3D risulta una tecnica produttiva estremamente efficace che racchiude in sé buone capacità produttive per volumi medio-bassi, veloce realizzazione di prototipi, riduzione degli scarti di produzione ed un¿eccezionale flessibilità e libertà progettuale con conseguente rimozione dei vincoli imposti dalle più comuni tecniche produttive. Se la stampa 3D in materiale polimerico risulta già altamente competitiva sul mercato grazie ai bassi costi di investimento richiesti per i macchinari, ciò non risulta altrettanto vero per i prodotti in metallo che a causa delle tecnologie impiegate richiedono apparecchiature complesse e costose. Gli elevati costi di investimento si riflettono negativamente sul costo del prodotto finito rendendo i componenti metallici stampati 3D ancora poco diffusi sul mercato. Lo scopo del presente lavoro è quello di proporre una via alternativa alla produzione di componenti in metallo che consenta di mantenere i vantaggi della manifattura additiva abbattendo però i costi di investimento e di conseguenza i costi del prodotto finito. Si intende raggiungere tale scopo accoppiando la tecnica FDM (Fused Deposition Modelling), già ampiamente usata per stampare polimeri termoplastici, con le tradizionali tecniche di debinding e sinterizzazione. Un filamento polimerico altamente caricato con polveri metalliche viene estruso attraverso la tecnica FDM per stampare l¿oggetto desiderato. Una volta stampato, il componente green viene avviato alla rimozione del legante polimerico (debinding) e alla successiva sinterizzazione per densificare il prodotto metallico. Le prestazioni meccaniche dei sinterizzati saranno ottimizzate mediante la tecnica Design of Experiments.
La possibilità di produrre componenti metallici sfruttando la tecnica di manifattura additiva Fused Deposition Modeling (FDM), già largamente impiegata per la stampa di oggetti polimerici, congiuntamente con le tradizionali tecniche di debinding e sinterizzazione, porta con sé innumerevoli vantaggi dal punto di vista economico, ambientale e sociale.
Per quanto riguarda il fattore economico, le comuni tecniche di stampa 3D impiegate nella produzione di componenti metallici (SLM, EBM, ecc.) richiedono cospicui costi di investimento fino a 1 milione di dollari secondo i dati forniti da Markforged. Un impiego efficace della tecnica FDM a tale scopo consentirebbe di ridurre considerevolmente i costi di investimento considerando che le stampanti progettate per lavorare con filamenti polimerici caricati con polveri metalliche richiedono un investimento compreso tra i 60,000 e i 120,000 euro secondo i dati riportati da Pollen e Metal Desktop. Una riduzione dei costi di investimento sui macchinari implica di riflesso una riduzione dei costi del componente finito rendendolo più competitivo sul mercato.
Dal punto di vista ambientale, l¿impiego della FDM consentirebbe di ridurre gli scarti di produzione e il consumo energetico rispetto alle comuni tecniche produttive come la stampa ad iniezione [1], ma anche di ridurre il consumo energetico rispetto alle tecniche di stampa 3D per i metalli come la sinterizzazione laser diretta (DMLS) e la deposizione diretta di metallo (DMD) [2].
Infine, dal punto di vista sociale, la possibilità di produrre componenti metallici personalizzati a costo ridotto consentirebbe di incrementare la platea di consumatori che possono accedere al prodotto. Ciò risulta fondamentale in settori quali ad esempio il biomedicale e il prostetico in cui la produzione ad hoc del dispositivo medico necessario consentirebbe di migliorare significativamente la qualità di vita del paziente.
Se i vantaggi della stampa FDM rispetto ai comuni processi produttivi e alle tecniche di stampa 3D per i metalli risultano evidenti, è anche necessario evidenziare che la qualità dei prodotti ottenuti con questa tecnica non è attualmente confrontabile con quella ottenibile con le altre tecniche. In particolare, l¿elevata difettosità del prototipo stampato, dovute ad esempio a residui polimerici, e l¿elevata porosità sono responsabili di scarse proprietà meccaniche [3] che necessitano di essere migliorate per raggiungere gli elevati standard richiesti soprattutto nell¿ambito biomedicale. Alla luce di ciò, lo scopo del presente progetto di ricerca è quello di procedere ad una massimizzazione delle proprietà meccaniche del componente stampato attraverso l¿ottimizzazione dei principali parametri di stampa e di processo, che influenzano difettosità, porosità e microstruttura, attraverso la tecnica statistica Design of Experiments (DoE). Lo studio sarà effettuato su vari metalli al fine di valutare l¿idoneità di ognuno di essi per il processo produttivo proposto e al fine di ottimizzare le proprietà meccaniche di ognuno (trazione, flessione, ILSS, ecc.) attraverso la modifica di parametri di processo fondamentali quali: direzione e temperatura di stampa, portata di materiale estruso, spessore dello strato stampato, ecc.
[1] Kreiger M, Pearce JM. Environmental Life Cycle Analysis of Distributed Three-Dimensional Printing
and Conventional Manufacturing of Polymer Products. ACS Sustain Chem Eng 2013;1.
doi:10.1021/sc400093k.
[2] Liu Z, Jiang Q, Ning F, Kim H, Cong W, Xu C, et al. Investigation of Energy Requirements and Environmental Performance for Additive Manufacturing Processes. Sustainability 2018;10. doi:10.3390/su10103606.
[3] Ilmiah A, Supriadi S, Whulanza Y, Saragih AS. Additive manufacturing of metallic based on extrusion
process¿: A review. J Manuf Process 2021;66:228¿37. doi:10.1016/j.jmapro.2021.04.018