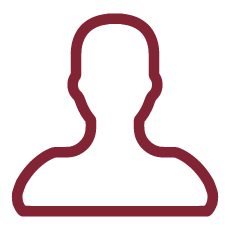
Le turbine a gas sono utilizzate fin dal 1791 in un¿ampia varietà di applicazioni tra cui propulsione di aerei, propulsione marina e generazione di potenza (heavy duty). I componenti di questi motori sperimentano sollecitazioni e temperature molto elevate in ambienti di gas altamente corrosivi e ossidanti, e sono tenuti a conservare le loro proprietà meccaniche per migliaia di ore di servizio.
Oltre alla presenza di meccanismi di ossidazione e corrosione a caldo, le elevate temperature contribuiscono al degrado delle proprietà strutturali del componente e danno luogo a sforzi termo-meccanici legati ai gradienti di temperatura ed ai diversi coefficienti di dilatazione termica dei materiali utilizzati. In quelle applicazioni in cui le temperature di esercizio sono compatibili con le proprietà termomeccaniche dei materiali utilizzati, le palette di turbina vengono rivestite per garantire la protezione da fenomeni di ossidazione ad alta temperatura e corrosione a caldo.
Lo scopo del presente progetto è quello di realizzare e caratterizzare un rivestimento innovativo che possa aumentare le prestazioni dei componenti in termini di temperatura massima di esercizio, mantenendo i costi di produzione invariati. A tal proposito sarà proposta e studiata una modifica del processo industriale di fabbricazione dei rivestimenti utilizzato attualmente (alluminizzazione per diffusione) con le caratterizzazioni microstrutturali e ad alta temperatura che ne conseguono, sottolineando la maggiore resistenza ad ossidazione dei componenti ottenuti attraverso il processo innovativo.
Con il termine electroless plating si fa riferimento ad una tecnica di deposizione autocatalitica che avviene per via prettamente chimica, in assenza di corrente elettrica. Le prime pubblicazioni su tale tecnica sono ad opera di Brenner e Riddel i quali per primi coniarono il termine electroless plating. La deposizione avviene per riduzione selettiva di ioni metallici sulla superficie del substrato, creando uno strato anch¿esso catalitico: per questo la deposizione electroless viene detta anche autocatalitica. Operando in assenza di una sorgente di energia elettrica, è necessaria la presenza di un agente riducente all¿interno della soluzione che, ossidandosi, metta a disposizione degli elettroni per la riduzione dello ione metallico. Ne deriva un rivestimento con spessore molto uniforme, che non produce ispessimenti in prossimità degli spigoli, cioè dove si concentra il campo elettrico. Inoltre, non si ha la necessità di lavorare con substrati conduttivi. L¿ipofosfito di sodio è il riducente più utilizzato tanto da essere adottato industrialmente per produrre rivestimenti anti usura o per rivestimenti di finitura. I bagni utilizzati sono sia a ph acidi che basici, e nel caso dei bagni acidi si raggiungono delle velocità di deposizione di decine di µm/h. Quello che viene depositato è una lega di nichel e fosforo. Per le applicazioni ad alta temperatura di nostro interesse è necessario depositare del nichel quanto più puro possibile, poiché il NiP presenta una fase liquida alle temperature caratteristiche del processo di alluminizzazione, inoltre, il fosforo potrebbe peggiorare la vita utile del rivestimento finale. A tal proposito, si è scelto di utilizzare come agente riducente l¿idrazina, nella sua forma più stabile monoidrata. Sebbene in letteratura siano presenti alcuni rivestimenti ottenuti mediante electroless plating con idrazina, la violenta reattività dell¿idrazina la rende inutilizzabile per deposizione ad alto spessore, come nel caso del seguente progetto. A tal proposito, l¿idea è quella di creare un reattore in-situ mediante complessazione dell¿idrazina con un reattivo carbossilato; tale complesso, stabile in soluzione, è in grado di complessare ulteriormente il nichel. In questo modo, limitando la reattività dell¿idrazina, sarà possibile ottenere deposizioni di nichel con spessori di circa 20 µm. Nella seconda parte della fase di studio della deposizione, le nanoparticelle di -Al2O3 saranno inserite all¿interno del bagno di deposizione. Per mantenere la loro dispersione omogenea, le particelle saranno sonicate con una sonda ad alta frequenza per evitare l¿agglomerazione una volta inserita in fase acquosa.
I rivestimenti così ottenuti saranno caratterizzati mediante microscopia elettronica ed infine i migliori rivestimenti in termine di spessore e distribuzione di particelle di allumina saranno alluminizzati mediante processo di pack cementation.