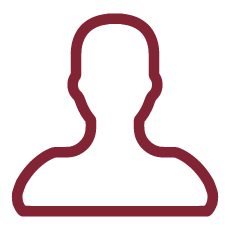
Biomechanical loads on body joints are the cause of non-fatal occupational problems, known as musculoskeletal disorders (MSDs). The spread of MSDs at work causes the increasing of days off, disabilities, and costs, for both companies and workers. The aim of this research project is the design of an innovative personal protective equipment (PPE) to introduce in working setting, to improve risk management and assessment at work. The PPE will be developed by leveraging wearable technologies, which allow to obtain reliability of dynamic and kinematic measurements and guarantee ergonomics evaluation in real time.
The aim is to realize a personal protective equipment for workers, composed of wearable sensors, with specific features, such as light-weight, low cost, designed not to hampering workers during their working activities. These sensors will allow us to measure kinematic and dynamic parameters related to upper and lower body segments, to define indices or personalized thresholds, considering information about workers, e.g. anthropometric measurements, physical parameters and previous accidents or pre-existing musculoskeletal disorders and disabilities. Moreover, several aspects of their own working activities will be considered, such as time working, loads and tools usually handled, and the conditions of their working environment. The adoption of these new technologies will guarantee to assess biomechanical parameters in real time, preserving the ecological aspects of the motor task and improving the safety of workers. The biomechanical parameters could be sent to an ergonomist or directly to the workers and stored in a cloud system or in a smartphone app.
Merging these biomechanical parameters and the information about workers will guarantee the improvement of risk management in terms of shifts and working hours. Thus, if a worker feels pain on the back while performing lifting task, he/she can be replaced by a colleague, or taking a break or continue to work, but performing tasks, which do not expose him/her to the same level of risk. The personal protective equipment (PPE) could be designed as a smart full suit or a set of smart clothing, such as t-shirt, pants, and socks, to be suitable to the working activities and to the motion analysis. The smart PPE will be integrated with several sensors to reconstruct the kinematic chain and the motor tracking of the workers and provide measurements of external forces, as ground reaction forces (GRFs), and balance parameters related to the center of pressure. According to our aim, the assessment of these parameters will guarantee to quantify the biomechanical load on L5/S1 joint, but also on the upper and lower limb joints, which are extremely engaged in manual material handling tasks. Moreover, the inertial sensors provide measurements of angles range of motion, which will be considered to set thresholds and discriminate postural patterns and tasks. The balance parameters obtained from the sensors placed on the socks, or on the full smart suit, will give information on the stability of the subject preventing fall risks, e.g. missteps descending stairs, during the working activities. The placement of the sensors in the smart PPE must be carried out avoiding the displacement of the sensors during the motion task.
A sensor-segment calibration must be implemented to correctly align sensors to the body segments, avoiding errors during the motor tracking and will be based on two tasks easy to perform by the workers before starting their working job, or when they decide to restart their activities after a break. Considering all these aspects, the PPE will be a wireless system with a low weight rechargeable batteries system, which will guarantee a continuous posture monitoring for more than three hours. Regarding the data acquisition and recording system, a software will be projected through visual programming system, even for designing an easy-to-use user interface. After the acquisition of the raw sensors data, an existing biomechanical model will be fed with them and anthropometric measurements of the workers, to reconstruct the orientation and position of each body segments in the 3D space. Obviously, for the implementation of the inverse dynamic method, which allow us to measure and quantifying loads on body joints, the measurements relating to the GRFs will be necessary. According to this need, small commercial load cells will be added to the PPE, integrating them into the worker shoes, or resistive or capacitive sensors that can be applied on a fabric creating a smart sock. The choice about the two possible solutions will be assessed considering the cost, for their designing and applicability, the durability of the elements and their resistance, the reliability of the measurements and easy to use by workers. The smart PPE will be realized with a fabric for guaranteeing not only comfort in terms of wearability, but also thermal comfort, considering the environmental conditions in which the system will be used. Moreover, the structure of the smart PPE must ensure a high protection of the sensors, to cushion shocks with elements present in the working environment that can damage them by limiting their functionality.